What material is PBT
Polybutylene terephthalate (PBT), also known as polybutylene terephthalate (PBT) in English, belongs to the polyester series. It is a crystalline thermoplastic polyester resin made by polycondensation of 1.4 PBT butylene glycol with terephthalic acid (PTA) or terephthalate (DMT), and is mixed through a mixing program to produce a milky white translucent to opaque thermoplastic resin. Together with PET, it is collectively referred to as thermoplastic polyester or saturated polyester.
Poly (butylene terephthalate), also known as poly (tetramethylene terephthalate). English name; Polybutylenetephthalate. Abbreviated as PBT PBTP or PTMT, it is a condensation polymer of p-benzoic acid and 1,4-butanediol. It can be prepared by ester exchange or direct esterification through condensation polymerization, and the future development trend is direct esterification production. PBT and PET are collectively referred to as thermoplastic polyester.
The PBT main chain is composed of saturated linear molecules connected by a rigid benzene ring and a flexible fatty alcohol in each repeating unit. The high geometric regularity and rigid part of the molecules endow the polymer with high mechanical strength, outstanding chemical resistance, heat resistance, and excellent electrical properties; There are no side chains in the molecules, and the structure is symmetrical, meeting the requirements of tight stacking, resulting in this polymer having a high crystallinity and high melting point. The molecular structure determines that PBT has good comprehensive performance. PBT is one of the latest and fastest growing varieties of engineering plastics in terms of industrialization. The reason why it has become a rising star in engineering plastics lies first in its excellent comprehensive performance, as well as its good formability and performance/price comparison. Therefore, although PBT plastic was not industrialized until the 1970s, it quickly sold well in the market and is now the fastest growing one of the five major engineering plastics.
1. Excellent mechanical performance, high mechanical strength, good fatigue resistance and dimensional stability. Creep is also small, and these properties rarely change under high temperature conditions.
The energy consumption for producing PBT is the lowest among engineering plastics, which is of great significance in the context of energy scarcity worldwide.
3. Excellent heat aging resistance, with an enhanced UL temperature index of 120-140 ℃. In addition, outdoor long-term aging resistance is also very good.
4. Good solvent resistance, no stress cracking.
PBT is easy to flame retardant and can reach UL94V-0 level. Due to its good affinity with flame retardants, it is easy to develop reactive or additive flame retardant grades. Flame retardant products are widely used in the electronic and electrical industry.
6. PBT is prone to decomposition when exposed to water in high temperature and humidity environments, and should be used with caution.
7. Excellent electrical performance, high volume resistivity and dielectric strength, excellent arc resistance, minimal moisture absorption, and stable electrical performance in humid and high-temperature environments. It is an ideal material for manufacturing electronic and electrical components.
8. Easy to shape and process, easy to use ordinary equipment for injection molding or extrusion. Due to its fast crystallization speed, good fluidity, and lower mold temperature requirements compared to other engineering materials, it only takes a few seconds to process thin-walled parts, which is crucial for large
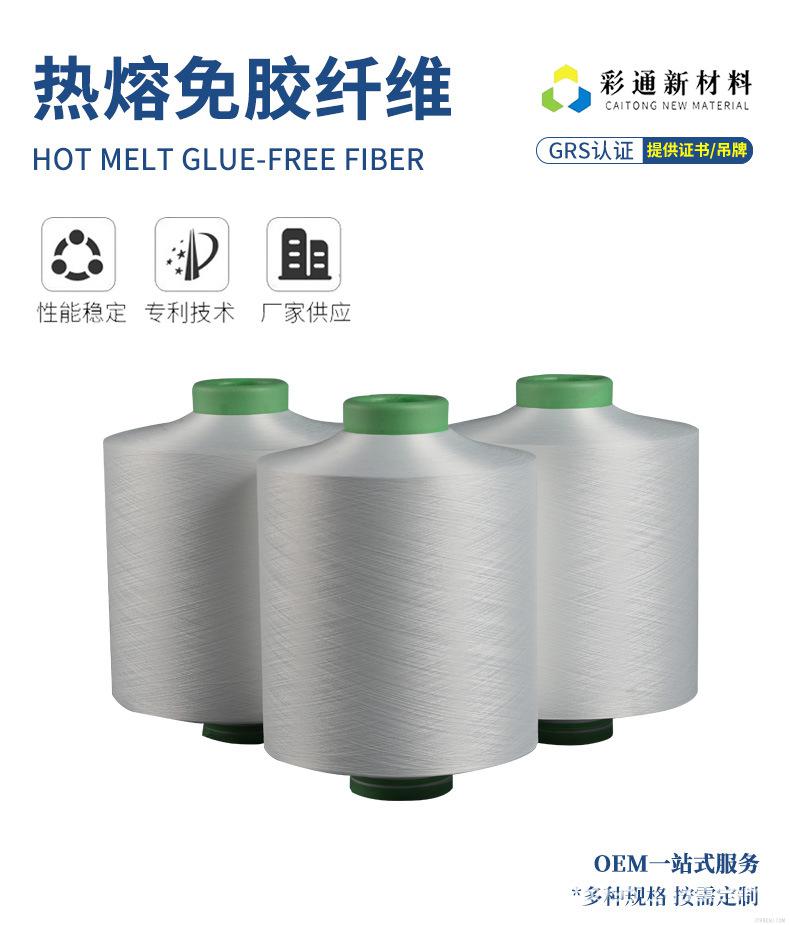